Keywords: helico axial two-phase flow pump generation liquid velocity control improved performance efficacy efficiency
In the following, the terms “pumping” and “compression” are used indifferently in the case of a two phase flow. When the liquid fraction is small (wet gas) the terminology “compression” is preferred while when the gas fraction is small (bubbly liquid) the terminology “pumping” is preferred. Obviously, in between, the two terminology may be used. Also “Impeller” and “Wheel” but also “Rectifier” and “Diffuser” are used indifferently. The term “Hydraulic cell” is used to define the assembly of an impeller and a diffuser.
Single phase flow machines – Their limit
The monophasic compression of a fluid (liquid or gas) can be carried out using volumetric (pistons, lobes, diaphragms) or rotodynamic machines. If the first type can be used for the compression of a two-phase mixture with a fairly good efficiency, these machines have many drawbacks in terms of mechanical excitations, size, weight and maintenance. The second type mainly includes radial and axial machines. These machines can possibly be used for two-phase compression but within extremely small ranges, in particular, when the gas rate is very low or on the contrary very high. In other words, they can only be used when the mixture is almost monophasic.
These machines cannot be used for the compression of a two-phase mixture due to the strong phase separation generating important interfacial and viscous losses inside the hydraulic cells as well as very high losses at the entrance of an impeller (the rotating part mounted on the drive shaft) or of a rectifier (the fixed part mounted on the stator) due to a large velocity difference between the two phases (angle of incidence at the entrance very different for each phase). Compared to single-phase performances, it is agreed to say that the two-phase “efficacy” is very low, this parameter measuring the ratio between the manometric head after compression of a two-phase fluid and the one which would be obtained in the case of a monophasic fluid (based on the same equivalent volumetric mass).
Helico axial design – First generation hydraulic
To this end, during the 1980s, the French Petroleum Institute (today IFPEN) has developed a hydraulic cell called Poseidon including two helico axial components (wheel and diffuser). This type of hydraulics presents several advantages. It allows, unlike positive displacement pumps, to operate continuously (without recycling) whatever the gas fraction is (from a fully gaseous phase to a fully liquid phase) and to reduce to some degree the phase separation, therefore, reducing a part of the losses mentioned above.
This type of hydraulics nevertheless presents some disadvantages. The principle of operation requires only very slightly curved impeller blades to reduce the transverse separation of the two phases with very different densities. Consequently, these blades are very long to achieve an acceptable pressure coefficient. By virtue of their constitution, these blades generate high viscous losses, greatly penalizing the efficiency (monophasic and consequently diphasic). The second disadvantage concerns the two-phase efficacy which, although it is higher than the one of a conventional single-phase machine, tends to decrease sharply when the difference in densities is pronounced. However, it should be noted that the hub of the impeller presents a concave curved shape (vertex directed towards the centre of the impeller). This configuration has the advantage of counteracting the residual centrifugal force and somewhat favouring the mixing of the phases up to a gas fraction of the order of 1 or 2. This gas fraction is expressed by the ratio of the volume flow rates of the gas and the liquid phases also designated by GLR for Gaz Liquid Ratio. Beyond this value, the phase separation increases, causing high energy losses. Below are some references:
S.Y. Li, X.P. Jiang, Jiambo Zhang – The two-phase flow analysis of helico-axial oil-gas multiphase pump for offshore oil fields
https://www.researchgate.net/publication/326699320_The_two-phase_flow_analysis_of_helico-axial_oil-gas_multiphase_pump_for_offshore_oil_fields Falcimaigne, Brac, Charron, Pagnier, Vilagines – Multiphase Pumping: Achievements and perspectives
https://pdfs.semanticscholar.org/7bc6/84d33f0a8ce107a028cd7f6a1d91e87a8517.pdf
J. Falcimaigne, S Decarre – Multiphase Production: Pipeline Transport, Pumping and Metering
https://books.google.fr/books?
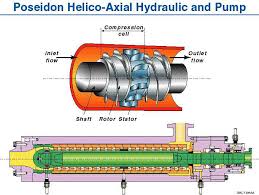
_https://images.app.goo.gl/ADzadNKgDQvMQLj87
This helico axial hydraulic cell can be designated by the “First generation cell”. It should be emphasized that this cell is strictly axial (cylindrical) on its external part.
This section will be completed during 2020 with a text describing the operation and the dimensioning method of a helico axial impeller (Poseidon or similar) for two-phase compression.
Attempts to use semi radial designs
Attempts have been made, in the past, to increase the compression ratio of a two-phase machine using semi-radial hydraulic cells while keeping the helical principle for the impeller. This type of machine did not meet expectations.
Why do these two types of two-phase machines malfunction when the gas rate is intermediate (fully diphasic) ? The reasons are as follows:
– in a strictly helico axial impeller, the liquid phase lags behind the gas phase due to the a difference in wall friction between the two phases (phase velocity determined by viscosity and density). The same phenomenon is observed in an axial impeller or in a horizontal duct.
– In a helico axial semi-radial impeller, the liquid phase is ahead of the gas phase due to the application of a large force (of centrifugal origin) exerted from the inlet to the outlet of the impeller. This force is all the more important as the external part of the impeller (the cover or the casing) is inclined (diameter at the outlet significantly greater than that of the inlet). The same phenomenon is observed in a radial impeller or any centrifugal element.
Liquid phase velocity control – New design
It is based on these observations that a helico “quasi-axial” impeller was developed during the 2010s. The term “quasi-axial” is used to suggest a slight inclination of the external part of the impeller (cover or casing). This external profile is designed to control the liquid velocity so as to keep it as close as possible to that of the gas phase. The principle is as follows: the combination of centrifugal and centripetal forces (Coriolis) results in a force directed in the centrifugal direction (described in the attached document). A radial force is exerted on the two phases of the mixture with a tangential component (along the external profile) which depends on the densities of the two phases and on the angle of the external profile.
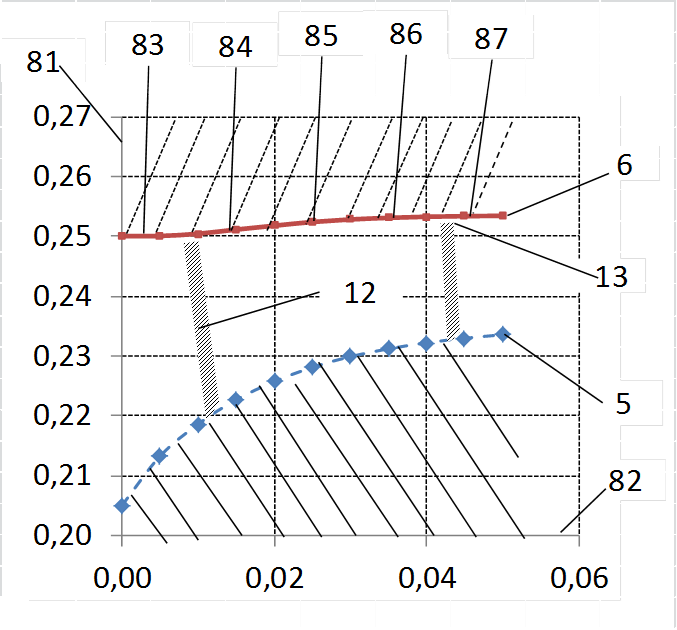
The external profile presents two curved shapes. In direction of the flow, a first concave section (apex directed towards the centre of the impeller) aimed at accelerating the liquid phase and a second convex one (apex directed towards the outside of the impeller) aimed at maintaining the velocity of the liquid phase as close as possible to the one of the gas phase. Without going into detail, this equality of velocities is obtained by balancing the friction forces and the component of the residual centrifugal force applied along the external profile.
Defining the interfacial slip as the difference in velocities between the liquid and gas phases, one can designate this impeller by “Interfacial Slip Control” (ISC) or “Phase Velocity Control” (PVC). This helico “quasi-axial” hydraulic cell can also be designated by a “Second generation cell”.
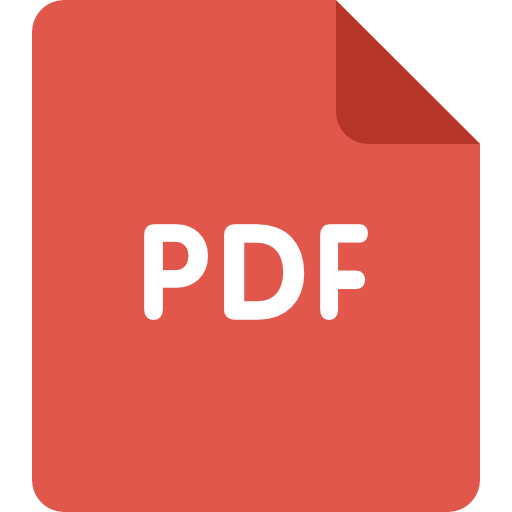
Summary for New Helico Radio Axial Impeller with “Phase Velocity Control” –
Patent for New Helico Radio Axial Impeller with “Phase Velocity Control” –
Patent figures for New Helico Radio Axial Impeller with “Phase Velocity Control” –
Comparison between HRA hydraulics – First and second generation, without and with “Phase Velocity Control”