Keywords: structured surfaces three-dimension structures two-orthogonal waves flow drag reduction turbulent turbulence
Adding a normal wave to the transverse wave
Two dimension structured surfaces have shown the capability to provide a flow drag reduction of the order of 10 %. This flow drag reduction is lower in the case of riblets with a triangle shape (5 to 6%) and larger in the case of riblets with a knife blade shape (10 to 12%). These performances were calculated with a RANS code and found in line with experiments carried out in the past by numerous workers. See web page on “2D structured surfaces”.
http://yvcharron.com/index.php/two-dimension-structures/
A three dimension structure surface – Type 1 including two flow drag reduction mechanisms has been analysed. These mechanisms are: a 2D structured surface associated with a transverse oscillating flow (wave). The resulting flow drag reduction is of the order of 20% at the optimum condition. These performances were determined with a LES code. See web page on “3D structured surfaces – Type 1”.
_http://yvcharron.com/index.php/three-dimension-structured-surfaces-type-1/
A new shape of 3D structured surface (Type 2) is proposed to provide a greater flow drag reduction. This type 2 includes two orthogonal oscillating waves, one parallel to the structured surface (as per type 1) and a new one normal to the structured surface and oriented in the flow direction. As very little calculation has been performed with this type of 3D structured surface, a phenomenological analysis is provided below to explain the mode of operation of the different types of riblets: 2D longitudinal riblets and 3D riblets, types 1 and 2.
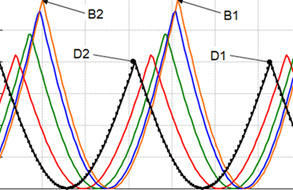
Potential of the integration of a third flow drag reduction mechanism
A LES Code could establish the mechanism of drag reduction provided by a plate oscillating transversely to the main flow direction. The maximum flow drag reduction was obtained for a dimensionless period of 100. In this specific case, the drag reduction tends to increase with the amplitude of the oscillation, disregarding the energy required to move the plate.
2D riblets of the knife blade type provide a maximum drag reduction of the order of 10 %. The same result was found with RANS and LES codes (see corresponding Web site pages).
3D structured surfaces (Type 1) combining the above two flow drag reduction mechanisms (2D riblets and transposed transverse flow oscillation) provide a drag reduction of the order of 20 % according to the LES code validated with the oscillating plate and 2D riblets. The maximum drag reduction was achieved for a dimensionless period of 100 and a maximum angle of the transverse oscillation of the order of 10 degrees.
It is anticipated that further drag reduction could be obtained by adding a second oscillating wave oriented in the flow direction and orthogonal to the transverse wave. This second wave (normal wave) could be of a sine wave type with a frequency equal to twice the transverse wave frequency. This normal wave would provide a riblet height increase at the crests of the transverse wave and a riblet height decrease at the inflexion points of the transverse wave. This should provide several advantages:
- A better control of the low speed streaks at the transverse wave crests
- Less viscous losses at the inflexion points of the transverse wave
- An additional parietal oscillating effect provided by the normal wave.
This optimum dimension values (h+ and S+) obtained during the 2D riblet calculations (flow simulation with RANS code) should be reviewed in relation with 3D riblets whatever they are of type 1 (A single oscillating wave) or type 2 (Two oscillating waves). Once a complete optimisation study has been carried out, it is expected to get a flow drag reduction significantly greater than 25 per cent.